Overview of Project Management in Civil Engineering
Project management in civil engineering is the cornerstone of delivering successful infrastructure projects. It involves coordinating various processes, from feasibility studies and planning to execution and final delivery. These projects are often complex, involving large budgets, extensive timelines, and multiple stakeholders. A project manager’s role includes overseeing schedules, budgets, and quality while ensuring compliance with safety standards and regulatory requirements. Without effective project management, even minor errors can cascade into significant delays, cost overruns, or structural defects.
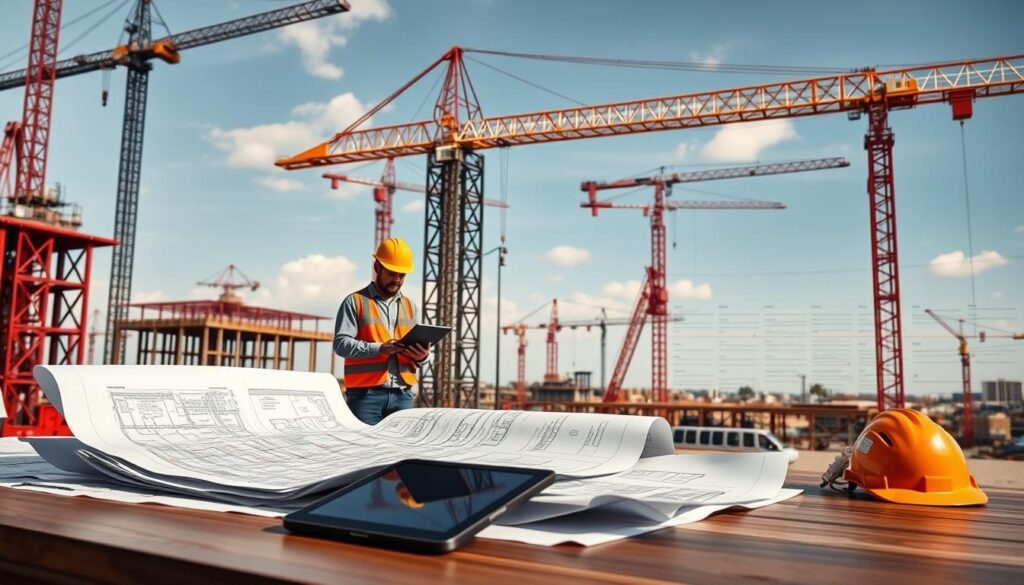
Importance of Avoiding Mistakes
Avoiding common mistakes in project management is not just about staying on schedule or within budget—it directly impacts the quality and safety of the final structure. Errors in resource allocation, risk assessment, or communication can lead to long-term financial and reputational damage. For example, a poorly planned project may result in structural instability, requiring costly repairs or risking human lives. By understanding these pitfalls, project managers can anticipate challenges and implement preventative measures to ensure a successful project outcome.
Understanding the Scope of Civil Engineering Project Management
Civil engineering projects are complex and need careful planning. Construction project planning is key to finish projects on time and within budget. It involves setting clear goals and identifying who needs to be involved.
Project scheduling is also vital. It means making a detailed plan of all steps, from start to finish. This helps ensure tasks are done well and on schedule.
Key Components of Project Management in Civil Engineering
- Scope definition
- Time management
- Cost control
- Quality assurance
- Resource allocation
- Risk management
Knowing these parts helps civil engineering projects succeed. Good construction project planning and project scheduling are key to this success.
The Role of Project Managers in Civil Construction
Project managers oversee everything from start to finish. They need strong leadership and communication skills. This ensures the team works together towards the project’s goals.
Critical Success Factors in Project Execution
Good communication and managing stakeholders are essential. Being able to adapt to changes is also critical. These factors help project managers overcome any challenges and complete projects successfully.
Key Topics Covered in This Article
Section | Sub-Section | Key Points Covered |
---|---|---|
Introduction | Overview of Project Management in Civil Engineering | Importance of project management in civil engineering, challenges of complex projects, and need for avoiding common mistakes. |
Importance of Avoiding Mistakes | Impact of errors on safety, costs, deadlines, and reputation. | |
Planning Phase Mistakes | Inadequate Feasibility Studies | Importance of site assessments, evaluating technical, economic, and environmental viability; steps to ensure proper feasibility studies. |
Insufficient Risk Assessments | Common risks in civil engineering projects (e.g., weather, labor shortages); strategies for developing a risk register and contingency planning. | |
Poorly Defined Project Scope | Problems caused by unclear scope; steps to create a detailed project scope and control scope changes. | |
Budgeting and Cost Control Errors | Unrealistic Budget Estimates | Causes of inaccurate budgeting; importance of detailed cost analysis, contingency funds, and quantity surveys. |
Ignoring Contingency Reserves | Risks of skipping contingency funds; strategies for allocating and managing reserves. | |
Failure to Monitor Cash Flow | Consequences of poor cash flow management; tips for tracking cash flow, aligning payments with project milestones, and negotiating terms with vendors. | |
Scheduling Issues | Overlooking Critical Path Method (CPM) | Importance of identifying task dependencies and prioritizing critical activities; how CPM prevents delays. |
Unrealistic Timeframes and Deadlines | Risks of over-ambitious deadlines; benefits of realistic milestones and time buffers. | |
Neglecting Seasonal and Weather Factors | Examples of weather impacts on projects; strategies for planning schedules around seasonal challenges. | |
Communication and Coordination Flaws | Inefficient Stakeholder Communication | Consequences of poor communication; importance of centralized updates, regular meetings, and clear communication plans. |
Lack of Clear Roles and Responsibilities | Risks of unclear roles; tips for defining roles, creating organizational charts, and conducting progress reviews. | |
Failure to Address On-Site Coordination Challenges | On-site issues due to poor coordination; how to appoint coordinators, use digital tools, and maintain clear communication. | |
Resource Allocation Problems | Underutilization of Equipment and Labor | Problems caused by idle resources; strategies for resource scheduling, reviews, and efficient utilization. |
Overloading Key Team Members | Risks of overloading team members; importance of balancing workloads and supporting team communication. | |
Failure to Manage Material Delivery Schedules | Delays caused by poor material scheduling; tips for coordinating deliveries and managing lead times. | |
Quality Management Shortcomings | Ignoring Quality Standards and Codes | Risks of non-compliance with safety and quality standards; steps to ensure adherence to codes. |
Insufficient Quality Assurance Processes | Importance of QA protocols, inspections, and third-party audits for maintaining quality. | |
Failing to Conduct Regular Site Inspections | Consequences of missed inspections; importance of inspection checklists and timely issue resolution. | |
Risk Management and Safety Oversights | Overlooking Health and Safety Compliance | Examples of safety risks; importance of training, safety plans, and audits. |
Ignoring Potential Environmental Impacts | Environmental risks of construction; steps for conducting impact assessments and engaging stakeholders. | |
Delayed Response to Unexpected Challenges | Consequences of poor crisis management; importance of contingency plans and response teams. | |
Documentation and Record-Keeping Errors | Poorly Maintained Project Records | Impact of disorganized records; strategies for setting up document management systems and assigning responsibility. |
Lack of Updated As-Built Drawings | Importance of recording design changes; how to update drawings in real-time and store them for future use. | |
Inadequate Change Order Documentation | Risks of undocumented changes; use of standardized templates, stakeholder approvals, and proper logging. | |
Technology and Innovation Missteps | Resistance to Adopting Construction Software | Problems caused by outdated methods; benefits of adopting software like Procore, Primavera P6, and cloud-based platforms. |
Inefficient Use of Project Management Tools | Missteps in using tools partially; strategies for training, updating data, and appointing tool administrators. | |
Overdependence on Outdated Technology | Challenges of relying on outdated equipment and software; importance of audits, staying updated, and budgeting for upgrades. | |
Conflict and Crisis Management Failures | Escalating Disputes Instead of Resolving Them | Consequences of unresolved disputes; steps for setting up a conflict resolution process and involving mediators. |
Poor Handling of Unexpected Delays or Changes | Impact of poorly managed delays; importance of contingency plans, real-time updates, and aligning stakeholders. | |
Neglecting Team Morale During Crisis Situations | Consequences of low morale during crises; strategies for transparent communication, rewards, and providing mental health support. | |
Conclusion | – | Recap of common mistakes, strategies to avoid them, and the importance of delivering safe, sustainable, and efficient project outcomes. |
Planning Phase Mistakes
Inadequate Feasibility Studies
Imagine starting a project only to discover halfway through that the site conditions don’t support the design, or the project’s cost far exceeds the budget. These scenarios often stem from incomplete or rushed feasibility studies. This phase lays the foundation for the entire project by assessing whether it is technically, economically, and environmentally viable. Overlooking key details—like soil stability or utility access—can lead to severe complications during construction.
How You Can Avoid This:
- Work with specialists to conduct in-depth studies of site conditions, including soil tests, topography, and environmental impact.
- Use project data from past, similar developments to create realistic projections.
- Develop a comprehensive feasibility report that evaluates potential risks, project costs, and timelines before making critical decisions.
Why It Matters:
Getting this step right saves you from costly delays and design changes later on. Think of it as investing in a smooth, headache-free construction process.
Insufficient Risk Assessments
Every civil engineering project comes with risks—some predictable, others not so much. Whether it’s unexpected bad weather, labor shortages, or price hikes for materials, these risks can completely disrupt your project if not managed properly. Ignoring risk assessment is like setting out on a journey without checking for possible roadblocks ahead.
How You Can Avoid This:
- Create a “risk register” to document potential issues, their likelihood, and their impact. For example, list the chance of flooding at the site and how you’d mitigate it.
- Review risks regularly as the project progresses; new risks often emerge over time.
- Include contingency funds in your budget to handle unexpected challenges without panicking.
Think About This:
It’s not just about identifying risks; it’s about being prepared for them. A proactive approach will keep your project running smoothly, even when surprises happen.
Poorly Defined Project Scope
Ever been in a situation where a small change request snowballs into multiple new tasks, leaving the project over budget and behind schedule? That’s what happens when the project scope isn’t clearly defined. Without a clear scope, everyone involved—clients, contractors, and your team—might have different expectations, leading to confusion and disagreements.

How You Can Avoid This:
- Create a detailed scope document that outlines exactly what the project will include—and just as importantly, what it won’t include.
- Involve all stakeholders during the planning phase to make sure everyone agrees on the project’s objectives.
- Establish a formal process for managing scope changes so you can evaluate their impact on time, cost, and resources before giving the green light.
Why This Step Is Key:
A well-defined scope acts as your project’s roadmap. It keeps everyone on the same page and helps you avoid scope creep, which is one of the biggest culprits of delays and budget overruns.
Planning Phase Mistakes
Inadequate Feasibility Studies
Imagine starting a project only to discover halfway through that the site conditions don’t support the design, or the project’s cost far exceeds the budget. These scenarios often stem from incomplete or rushed feasibility studies. This phase lays the foundation for the entire project by assessing whether it is technically, economically, and environmentally viable. Overlooking key details—like soil stability or utility access—can lead to severe complications during construction.
How You Can Avoid This:
- Work with specialists to conduct in-depth studies of site conditions, including soil tests, topography, and environmental impact.
- Use project data from past, similar developments to create realistic projections.
- Develop a comprehensive feasibility report that evaluates potential risks, project costs, and timelines before making critical decisions.
Why It Matters:
Getting this step right saves you from costly delays and design changes later on. Think of it as investing in a smooth, headache-free construction process.
Insufficient Risk Assessments
Every civil engineering project comes with risks—some predictable, others not so much. Whether it’s unexpected bad weather, labor shortages, or price hikes for materials, these risks can completely disrupt your project if not managed properly. Ignoring risk assessment is like setting out on a journey without checking for possible roadblocks ahead.
How You Can Avoid This:
- Create a “risk register” to document potential issues, their likelihood, and their impact. For example, list the chance of flooding at the site and how you’d mitigate it.
- Review risks regularly as the project progresses; new risks often emerge over time.
- Include contingency funds in your budget to handle unexpected challenges without panicking.
Think About This:
It’s not just about identifying risks; it’s about being prepared for them. A proactive approach will keep your project running smoothly, even when surprises happen.
Poorly Defined Project Scope
Ever been in a situation where a small change request snowballs into multiple new tasks, leaving the project over budget and behind schedule? That’s what happens when the project scope isn’t clearly defined. Without a clear scope, everyone involved—clients, contractors, and your team—might have different expectations, leading to confusion and disagreements.
How You Can Avoid This:
- Create a detailed scope document that outlines exactly what the project will include—and just as importantly, what it won’t include.
- Involve all stakeholders during the planning phase to make sure everyone agrees on the project’s objectives.
- Establish a formal process for managing scope changes so you can evaluate their impact on time, cost, and resources before giving the green light.
Why This Step Is Key:
A well-defined scope acts as your project’s roadmap. It keeps everyone on the same page and helps you avoid scope creep, which is one of the biggest culprits of delays and budget overruns.
Budgeting and Cost Control Errors
Unrealistic Budget Estimates
Have you ever seen a project stall because the money ran out halfway through? Unrealistic budget estimates are often to blame. Civil engineering projects involve numerous variables—materials, labor, equipment, and more—all of which can change during the project. Estimating without factoring in these potential fluctuations leads to severe financial strain. For example, underestimating the cost of raw materials like concrete or steel can create major disruptions later on.
How You Can Avoid This:
- Conduct a detailed cost analysis during the planning stage, including historical data from similar projects.
- Use Quantity Surveyors (QS) to accurately estimate material, labor, and equipment costs.
- Include a contingency budget, typically 10–20% of the total project cost, to cover unexpected expenses.
Pro Tip:
Keep your estimates grounded in reality. Be conservative with costs rather than overly optimistic—you’ll thank yourself later when you avoid unpleasant surprises.
Ignoring Contingency Reserves
When budgets are tight, it’s tempting to skip setting aside a contingency fund, thinking everything will go as planned. But civil engineering projects rarely work out perfectly. Unexpected issues like equipment breakdowns, delays, or additional work requirements often arise. Without a financial buffer, you might find yourself scrambling to secure extra funding at the last minute.
How You Can Avoid This:
- Always allocate a contingency reserve based on the project’s complexity. For instance, a high-risk project might need a 20% reserve, while a straightforward project may only need 10%.
- Monitor contingency usage and ensure it is only spent on legitimate unforeseen issues.
- Avoid treating the contingency reserve as part of the primary budget—it’s there for emergencies, not routine expenses.
Why It’s Crucial:
Having a contingency fund can be the difference between a manageable setback and a full-blown crisis. It’s better to have extra funds left over than to halt progress due to insufficient resources.
Failure to Monitor Cash Flow
Even with a well-prepared budget, poor cash flow management can bring your project to a halt. For example, paying suppliers late or not tracking how money is spent can lead to delays in material delivery or strained relationships with contractors. Cash flow isn’t just about having funds—it’s about having them at the right time.
How You Can Avoid This:
- Set up a cash flow forecast that aligns payments to suppliers, labor, and other expenses with project milestones.
- Regularly track and update cash flow to identify potential shortfalls early.
- Negotiate payment terms with vendors and contractors to balance your cash flow.
Scheduling Issues
Overlooking Critical Path Method (CPM) Analysis
One of the most common reasons projects fall behind schedule is a lack of proper scheduling tools like the Critical Path Method (CPM). CPM helps project managers identify the longest sequence of tasks that must be completed on time to avoid delays. Ignoring this analysis can lead to mismanagement of key activities, causing bottlenecks and inefficiencies. For example, failing to prioritize foundational work before proceeding to structural tasks can disrupt the entire timeline.
How You Can Avoid This:
- Use CPM software or tools to map out critical tasks and their dependencies.
- Regularly review and update the critical path as the project progresses to account for any changes.
- Assign experienced personnel to manage critical path activities and monitor them closely.
Why It’s Essential:
A well-maintained critical path ensures that you stay focused on the most time-sensitive activities, reducing the risk of cascading delays.
Unrealistic Timeframes and Deadlines
Setting overly ambitious deadlines might look good on paper, but it often leads to stress, errors, and rework. Unrealistic timeframes are usually the result of pressure to deliver quickly or a lack of understanding of the complexities involved. For instance, a tight deadline might force workers to rush concrete curing, compromising structural integrity.
How You Can Avoid This:
- Consult with contractors, engineers, and other experts to create a realistic schedule based on past project experiences.
- Break the project into smaller, manageable milestones with achievable deadlines.
- Factor in time for potential delays caused by weather, equipment breakdowns, or other unforeseen events.
Think About This:
It’s better to deliver a quality project slightly later than to meet an impossible deadline with substandard results. Clients and stakeholders value durability and reliability over rushed work.
Neglecting Seasonal and Weather Factors
Weather plays a significant role in civil engineering projects, yet it’s often underestimated during scheduling. For instance, heavy rains during the monsoon season can halt excavation work, or extreme heat might limit the hours workers can spend outdoors. Ignoring such factors leads to missed deadlines and additional costs.
How You Can Avoid This:
- Research historical weather patterns in the project location to plan activities during favorable conditions.
- Build flexibility into your schedule to accommodate potential weather-related delays.
- Use advanced weather forecasting tools to make real-time adjustments to your plan.
Why This Matters:
Planning with weather and seasonal considerations in mind ensures your project stays on track without compromising safety or quality.
Communication and Coordination Flaws
Inefficient Stakeholder Communication
A lack of clear and consistent communication among stakeholders often leads to misunderstandings, conflicting instructions, and delays. In civil engineering projects, where multiple parties—clients, contractors, consultants, and suppliers—are involved, a misstep in communication can have ripple effects. For example, if design changes are not properly conveyed to site managers, the work may proceed based on outdated drawings, causing rework and wasted resources.
How You Can Avoid This:
- Establish a communication plan that outlines how updates, decisions, and changes will be shared with all stakeholders.
- Use project management tools to centralize communications, ensuring everyone has access to the latest information.
- Schedule regular meetings, both on-site and virtual, to keep everyone aligned on project goals and progress.
Why It’s Important:
Clear communication builds trust and ensures that everyone is working toward the same objectives. It also minimizes errors and disputes caused by miscommunication.
Lack of Clear Roles and Responsibilities
When team members aren’t sure of their specific duties, tasks can fall through the cracks or be duplicated unnecessarily. This lack of clarity can lead to inefficiency, frustration, and blame-shifting when problems arise. For example, if no one is explicitly assigned to monitor material deliveries, delays can occur without anyone taking accountability.
How You Can Avoid This:
- Develop an organizational chart that clearly defines roles, responsibilities, and reporting lines.
- Communicate these roles to the entire team at the start of the project and reinforce them as needed.
- Conduct regular progress reviews to ensure accountability and address any overlaps or gaps in responsibilities.
Why This Matters:
A well-defined structure keeps the project running smoothly by ensuring that every team member knows their role and can focus on their specific tasks.
Failure to Address On-Site Coordination Challenges
Even with a solid plan, poor coordination on the ground can disrupt progress. On-site challenges, such as delays in material delivery, overlapping tasks, or labor shortages, require real-time communication and quick decision-making. Without effective on-site coordination, small problems can escalate into larger issues.
How You Can Avoid This:
- Appoint a site coordinator to oversee day-to-day activities and resolve issues as they arise.
- Use digital tools to track progress and identify potential conflicts in real time.
- Maintain open lines of communication between on-site teams and off-site management to address problems promptly.
Consider This:
On-site coordination is where plans meet reality. Efficiently managing this dynamic environment is key to keeping the project on schedule and within budget.
Resource Allocation Problems
Underutilization of Equipment and Labor
It’s common in civil engineering projects to see expensive equipment sitting idle or workers waiting for the next task. This underutilization not only increases costs but also delays progress. For instance, if excavation equipment isn’t properly scheduled, it might sit unused while crews wait for site preparation to finish, wasting both time and money.
How You Can Avoid This:
- Develop a resource schedule that aligns equipment and labor availability with project milestones.
- Use tools like Gantt charts or resource management software to track utilization and ensure nothing is underused.
- Conduct regular reviews of resource allocation to adjust for changing project needs.
Why This Matters:
Every piece of equipment and every hour of labor costs money. Efficient utilization ensures that your project budget is spent wisely and avoids unnecessary delays.
Overloading Key Team Members
Sometimes, certain team members or specialists are tasked with handling too many responsibilities, leading to burnout, delays, and reduced productivity. For example, assigning the same engineer to supervise multiple sites might compromise the quality of oversight.
How You Can Avoid This:
- Delegate responsibilities evenly across your team based on expertise and availability.
- Identify potential bottlenecks in workloads and redistribute tasks before they become a problem.
- Encourage open communication among team members so they feel comfortable reporting when they’re overwhelmed.
Consider This:
A balanced workload keeps your team motivated and focused, leading to better performance and fewer errors. Overloading key personnel, on the other hand, can result in poor decision-making and costly mistakes.
Failure to Manage Material Delivery Schedules
Timely delivery of materials is critical in construction projects. Delays in receiving materials can bring work to a standstill, while early deliveries can cause storage issues or damage to sensitive materials. For instance, concrete delivered too early might harden before it’s used, resulting in waste and additional costs.
How You Can Avoid This:
- Coordinate with suppliers to schedule deliveries according to the project timeline.
- Monitor the lead times of critical materials and plan orders well in advance.
- Designate secure storage areas on-site for materials that need to be delivered early.
Why It’s Essential:
Efficient material management ensures that work progresses smoothly without interruptions, helping to maintain your schedule and budget.
Quality Management Shortcomings
Ignoring Quality Standards and Codes
Adhering to quality standards and building codes isn’t optional—it’s mandatory for safety, durability, and compliance. Ignoring these standards, whether due to cost-cutting or oversight, can result in structural failures, legal consequences, or even project shutdowns. For example, substituting low-grade materials to save money might lead to cracks in the foundation or compromised structural integrity.
How You Can Avoid This:
- Familiarize yourself with all relevant building codes, safety regulations, and industry standards applicable to your project.
- Ensure that your team is trained to follow these guidelines during all phases of the project.
- Conduct quality checks at every stage to confirm compliance with codes and standards.
Why It’s Critical:
Meeting quality standards protects the safety of future users, reduces the risk of legal liabilities, and enhances the reputation of your project and your team.
Insufficient Quality Assurance Processes
Without a robust quality assurance (QA) system in place, defects can go unnoticed until it’s too late. For example, if concrete isn’t tested for strength and durability before pouring, flaws might only become apparent after the structure is completed, leading to costly repairs or rework.
How You Can Avoid This:
- Establish clear QA protocols for every phase of the project, including material testing, inspections, and documentation.
- Assign dedicated QA personnel to oversee compliance and identify issues early.
- Use third-party auditors to provide an unbiased review of quality standards and practices.
Think About This:
Quality assurance isn’t just about identifying problems—it’s about preventing them. A proactive QA approach saves time, money, and resources in the long run.
Failing to Conduct Regular Site Inspections
Regular site inspections are essential to ensure that work is being carried out according to the project plan and quality standards. Skipping inspections or conducting them inconsistently can allow errors to compound. For instance, undetected flaws in rebar placement can weaken the structure and require costly corrections later.
How You Can Avoid This:
- Schedule regular inspections during critical stages of the project, such as foundation work, structural framing, and finishing.
- Use detailed inspection checklists to ensure all aspects are covered.
- Document inspection findings and address any issues promptly to avoid delays.
Why It Matters:
Frequent site inspections act as a safeguard against errors and ensure that quality is maintained throughout the project lifecycle. They also give stakeholders confidence that the project is progressing as planned.
Risk Management and Safety Oversights
Overlooking Health and Safety Compliance
Health and safety are non-negotiable in civil engineering projects. Neglecting safety protocols can lead to workplace accidents, injuries, or even fatalities, bringing work to a halt and exposing you to legal liabilities. For example, failing to provide proper fall protection equipment for workers on high-rise structures can result in severe injuries and lawsuits.
How You Can Avoid This:
- Develop a comprehensive safety plan that outlines procedures for all potential hazards, such as working at heights, operating heavy machinery, and handling hazardous materials.
- Ensure all workers receive safety training and are equipped with the necessary personal protective equipment (PPE).
- Conduct regular safety audits to identify and address any non-compliance or risks.
Why This Is Non-Negotiable:
Prioritizing safety protects workers, avoids delays caused by accidents, and ensures compliance with legal and industry standards. A safe work environment also fosters better productivity and morale.
Ignoring Potential Environmental Impacts
Civil engineering projects often impact the surrounding environment, from altering landscapes to affecting local ecosystems. Overlooking environmental risks can lead to regulatory penalties, community opposition, and long-term harm to the environment. For example, a poorly planned drainage system can cause flooding in nearby areas or contamination of water sources.
How You Can Avoid This:
- Conduct Environmental Impact Assessments (EIA) during the project planning phase to identify and mitigate risks.
- Implement eco-friendly construction practices, such as using sustainable materials and minimizing waste.
- Engage with local communities and stakeholders to address concerns and build trust.
Think About This:
Respecting the environment isn’t just about compliance—it’s about leaving a positive legacy. Environmentally conscious projects often gain more community support and add long-term value.
Delayed Response to Unexpected Challenges
Unexpected challenges—such as natural disasters, labor strikes, or sudden material shortages—are common in large projects. The issue isn’t the challenge itself but the inability to respond quickly and effectively. A delayed response can exacerbate the problem, increasing downtime and costs.
How You Can Avoid This:
- Develop a risk management plan with detailed contingencies for potential issues, such as alternative suppliers, emergency labor resources, or disaster recovery protocols.
- Assign a dedicated risk response team to monitor and address challenges as they arise.
- Maintain open communication channels to ensure all stakeholders are aware of issues and aligned on solutions.
Why It Matters:
Quick and decisive action minimizes disruptions and ensures the project stays as close to schedule and budget as possible, even in the face of challenges.
Documentation and Record-Keeping Errors
Poorly Maintained Project Records
Detailed and accurate documentation is the backbone of any successful civil engineering project. Poor record-keeping can lead to confusion, missed deadlines, and disputes with stakeholders. For instance, incomplete records of materials ordered and used might result in over-purchasing or running out of critical supplies.
How You Can Avoid This:
- Implement a structured document management system to track contracts, progress reports, material usage, and financial records.
- Assign specific team members to maintain and update records consistently.
- Use digital tools or software for document storage, making retrieval and sharing easy when needed.
Why It’s Important:
Proper documentation ensures transparency, accountability, and quick resolution of disputes. It also provides a valuable reference for future projects.
Lack of Updated As-Built Drawings
As-built drawings reflect the actual changes made during construction compared to the original design. Neglecting to update these drawings creates challenges in maintenance, repairs, or future expansions. For example, if underground utilities are relocated but not documented, it can cause significant issues for future excavation work.
How You Can Avoid This:
- Update as-built drawings regularly during construction to reflect changes in real time.
- Ensure that any modifications are reviewed and approved by relevant stakeholders before updating the drawings.
- Store updated drawings in an accessible format for easy reference in the future.
Think About This:
Accurate as-built drawings are a critical asset for both current and future use. They provide a clear understanding of what was built and how it deviates from initial plans.
Inadequate Change Order Documentation
Construction projects often require changes to the original plan, whether due to client requests, unforeseen conditions, or design errors. However, failing to document these changes properly can lead to disputes, additional costs, and delays. For example, a verbal agreement to modify a foundation design without formal documentation can cause confusion during billing or inspections.
How You Can Avoid This:
- Use formal change order templates to document all modifications, including descriptions, cost implications, and updated timelines.
- Require approval from all relevant stakeholders before implementing any changes.
- Maintain a clear log of all change orders to ensure accountability and prevent disputes.
Why It Matters:
Properly documented change orders keep everyone on the same page, avoiding misunderstandings and ensuring that all modifications are accounted for in the project scope, timeline, and budget.
Documentation and Record-Keeping Errors
Poorly Maintained Project Records
Have you ever found yourself scrambling to find crucial project details at the last minute? Poor record-keeping often leads to such stressful situations, resulting in delays, mismanagement, and even financial setbacks. Without organized records, tracking materials, progress, and financials becomes chaotic, increasing the risk of miscommunication and missed deadlines.
What You Can Do:
- Set up a structured document management system to centralize contracts, progress updates, and material inventories.
- Assign a specific team member or department to maintain and update records regularly.
- Use digital tools like construction management software to store, track, and access records easily.
Why It Helps:
Well-maintained records allow for better decision-making, transparency, and smooth coordination among all stakeholders. No more scrambling for data when you need it most!
Lack of Updated As-Built Drawings
Imagine completing a large project only to realize that changes made during construction weren’t documented. This lack of updated as-built drawings can create headaches during maintenance or future expansions. For example, if underground utilities were relocated but not recorded, digging in the wrong place later could cause damage and costly repairs.
How to Avoid This Issue:
- Update as-built drawings regularly during construction to reflect actual modifications.
- Ensure all changes are reviewed and approved by project stakeholders before being finalized.
- Store drawings in an easily accessible format for future use by maintenance teams or expansion projects.
Real-Life Impact:
Accurate as-built drawings are like a map for your project’s future. They ensure everyone knows exactly what’s been built and where, saving time, money, and frustration down the road.
Inadequate Change Order Documentation
Changes during construction are inevitable, whether due to client requests or unforeseen site conditions. But failing to document these changes properly can lead to confusion, disputes, and even financial losses. For instance, verbally agreeing to modify a foundation without formal documentation can cause billing disputes and inspection failures later.
Steps to Manage Change Orders Effectively:
- Use standardized templates to document every change, including descriptions, cost implications, and updated timelines.
- Get all changes approved by stakeholders before implementation to ensure clarity and accountability.
- Maintain a change order log to track all modifications in one place, making it easy to review and reference when needed.
Why It Works:
When every change is clearly documented and approved, there’s no room for miscommunication. You’ll avoid arguments and ensure everyone stays on the same page.
Technology and Innovation Missteps
Resistance to Adopting Construction Software
Relying on outdated tools for project management is a common issue in civil engineering projects. Avoiding modern construction software leads to inefficiencies, delays, and communication gaps. For instance, teams may struggle to stay aligned when there is no centralized system for tracking progress and updates.
What You Can Do:
- Adopt reliable project management software like Procore, Primavera P6, or MS Project for scheduling, budgeting, and collaboration.
- Train your team to utilize all features of the software to ensure its effective use.
- Implement cloud-based systems to allow real-time data sharing among all project stakeholders.
Result:
Using construction software streamlines workflows, enhances communication, and improves overall project efficiency.
Inefficient Use of Project Management Tools
Simply adopting project management software is not enough—underutilizing these tools can prevent you from reaping their full benefits. For example, using a scheduling tool without leveraging its cost-tracking or risk assessment features limits its impact on project success.
How to Avoid This Issue:
- Provide thorough training sessions to ensure every team member knows how to use the software’s full capabilities.
- Regularly update the software with project data to keep all information accurate and relevant.
- Assign a dedicated administrator to oversee the system, troubleshoot issues, and ensure consistent usage.
Impact:
Efficient use of project management tools improves decision-making, resource allocation, and project tracking, enabling teams to meet deadlines and budgets with greater precision.
Overdependence on Outdated Technology
Using outdated technology or equipment often leads to inefficiencies and compromises project quality. For instance, old surveying tools might result in inaccurate measurements, affecting the overall design and execution of a project.
Steps to Avoid This Mistake:
- Perform regular technology audits to identify tools and equipment that need upgrading.
- Stay informed about industry advancements by participating in trade shows, professional networks, or industry-specific training programs.
- Allocate resources for technology upgrades to improve productivity, safety, and project outcomes.
Outcome:
Upgrading outdated technology ensures accurate results, improves efficiency, and keeps your projects aligned with modern industry standards.
Conflict and Crisis Management Failures
Escalating Disputes Instead of Resolving Them
Disputes are inevitable in civil engineering projects, whether they arise between contractors, clients, or internal teams. However, letting these disputes escalate without timely resolution can lead to delays, increased costs, and strained relationships. For instance, disagreements over scope changes or billing can halt progress and affect morale on-site.
What You Can Do:
- Establish a conflict resolution process from the outset, including clear procedures for addressing disputes.
- Foster open communication among stakeholders to identify and resolve disagreements early.
- Involve neutral mediators or third-party arbitrators if conflicts cannot be resolved internally.
Impact of Effective Management:
Resolving disputes promptly helps maintain project momentum, keeps relationships intact, and prevents small disagreements from turning into costly delays.
Poor Handling of Unexpected Delays or Changes
Unexpected events, such as bad weather, labor strikes, or supply chain disruptions, can derail even the best-planned projects. Poorly managed responses to these challenges often exacerbate the situation, leading to prolonged downtime or budget overruns.
Steps to Handle Delays Effectively:
- Develop a contingency plan during the planning phase, accounting for potential risks and delays.
- Set up a crisis management team to monitor and address unforeseen challenges as they arise.
- Keep stakeholders informed with real-time updates to ensure everyone is aligned on the response strategy.
Why It’s Important:
A proactive approach to delays minimizes disruptions, keeps the project on track, and reassures stakeholders of the team’s ability to handle challenges.
Neglecting Team Morale During Crisis Situations
Crises often create high-stress environments, which can lead to burnout, reduced productivity, and even staff turnover if team morale is ignored. For example, expecting workers to meet deadlines during a material shortage without proper communication or support can create frustration and resentment.
How to Support Your Team:
- Maintain transparent communication about the crisis, explaining the challenges and proposed solutions.
- Recognize and reward team members who contribute extra effort during difficult times.
- Provide mental health support or additional resources to reduce stress and maintain motivation.
The Outcome:
A motivated and supported team is more likely to stay productive and collaborative, even during challenging times, ensuring the project’s success despite setbacks.
SUMMARY
Project management in civil engineering is a multifaceted process where avoiding common mistakes is essential to achieving successful outcomes. Key areas to focus on include thorough planning, realistic budgeting, and effective scheduling. Conducting detailed feasibility studies, performing risk assessments, and clearly defining the project scope can prevent early-phase errors that often lead to delays or cost overruns. Maintaining control over budgets through accurate estimates, contingency reserves, and cash flow monitoring ensures financial stability throughout the project. Scheduling must account for critical task dependencies and potential weather delays to avoid unrealistic timelines.
Communication and coordination are central to preventing mismanagement. Clear roles, open communication channels, and centralized updates help keep teams aligned. Efficient resource allocation, including the proper use of labor, materials, and equipment, minimizes waste and ensures smooth project execution. Adhering to quality standards through regular inspections, updated as-built drawings, and proper documentation of change orders safeguards the integrity and accuracy of the project.
Risk management is another critical component, requiring safety compliance, environmental assessments, and preparedness for unforeseen challenges. Leveraging modern project management tools and keeping technology updated enhances efficiency and accuracy. Finally, addressing disputes promptly, supporting team morale during crises, and maintaining transparent documentation allow projects to navigate complexities successfully. By prioritizing these practices, civil engineering projects can achieve timely, cost-effective, and high-quality results while maintaining safety and stakeholder satisfaction.
FAQ
1. What are the key components of project management in civil engineering?
Key components include defining the project scope, managing time, and controlling costs. Quality assurance, resource allocation, and risk management are also important.
2. What is the role of the project manager in civil construction?
The project manager oversees civil engineering projects. They manage stakeholders, communicate effectively, and adapt to changes.
3. What are the critical success factors in civil engineering project execution?
Success factors include clear communication and effective stakeholder management. Being able to adapt to changes is also key.
4. What are the types of risks in civil engineering projects?
Risks include technical, environmental, financial, and social risks.
5. How can a risk management plan be created for civil engineering projects?
A risk management plan involves identifying, analyzing, and prioritizing risks. Then, develop strategies to mitigate them.
6. Why is effective communication important in civil engineering projects?
Effective communication is essential. It involves stakeholders with different interests. Without it, misunderstandings and conflicts can arise.
7. What strategies can be used to manage stakeholder expectations in civil engineering projects?
Strategies include clear communication channels and documentation protocols. Addressing concerns proactively is also important.
8. How can budget overruns and financial mismanagement be prevented in civil engineering projects?
Preventing overruns requires robust financial management. This includes detailed cost estimation and regular budget reviews.
9. What are the key quality control measures in civil engineering projects?
Measures include setting standards, inspecting work, and testing materials. This ensures compliance with specifications and regulations.
10. How can effective timeline management be achieved in civil engineering projects?
Effective management involves using project management tools and techniques. Regular monitoring and updates of project schedules are also necessary.
Refrences
Project Management Institute (PMI). A Guide to the Project Management Body of Knowledge (PMBOK® Guide), 7th Edition. Project Management Institute, 2021.
- This guide offers comprehensive standards and guidelines for project management applicable across various industries, including civil engineering. PMI PMBOK® Guide
American Society of Civil Engineers (ASCE). Construction Site Management Practices Handbook. ASCE Publications.
- This handbook provides detailed practices for managing construction sites effectively, focusing on avoiding common pitfalls in civil engineering projects. ASCE Construction Site Management Practices Handbook
International Organization for Standardization (ISO). ISO 21500:2012 Guidance on Project Management.
- ISO 21500 offers guidance on concepts and processes of project management that are important for the performance of projects. ISO 21500:2012
Hendrickson, C. Project Management for Construction: Fundamental Concepts for Owners, Engineers, Architects, and Builders. Carnegie Mellon University.
- This resource focuses on project management principles specific to construction and civil engineering, providing practical insights for professionals. Project Management for Construction
Kerzner, H. Project Management: A Systems Approach to Planning, Scheduling, and Controlling, 12th Edition. Wiley, 2017.
- This book explores project management tools, scheduling methods, and risk management techniques in detail, applicable to large-scale engineering projects. Project Management by Harold Kerzner
Occupational Safety and Health Administration (OSHA). Construction Industry Standards and Resources.
- OSHA provides critical resources for ensuring safety compliance on construction sites, which is essential for project managers in civil engineering. OSHA Construction Standards
Quickbase. “The 6 Construction Project Management Best Practices.”
- This article discusses best practices for construction project management, including managing expectations, thorough documentation, and effective communication. Quickbase Best Practices